Technical Details
Photo credit: sturti/E+ via Getty Images
The Facts about PVC – Part II
Roofing contractors can be confident in recommending PVC systems to their customers. Photos courtesy of Mule-Hide Products Co.
Tapping a Wide Array of Options to Meet Project Demands
By Tony Vieira
PVC roofing systems are a favorite choice of architects, consultants and other design professionals. Part I of this series shared the reasons why, from PVC’s exceptional chemical resistance and unmatched fire resistance to its energy efficiency and 50-year track record of successful use worldwide.
PVC is also a highly versatile solution that can be tailored to meet a wide range of needs. This article will highlight the array of membrane types, installation methods, and warranty choices available.
Attachment Methods
PVC roofing systems can be fully adhered to, mechanically attached, or induction welded.
Most PVC roofing systems are fully adhered to. This typically provides the longest and highest manufacturer wind speed warranty options and the highest FM (Factory Mutual) ratings.
Induction-welded systems, in which specialized equipment is used to weld the membrane to PVC-coated plates installed directly underneath, are quick to install and cost-effective. They also allow the crew to quickly dry in a roof; once the membrane has been secured, the crew can weld the seams to keep the weather out and then return to weld the remaining plates.
Mechanically attached systems are often the fastest and lowest in cost to install.
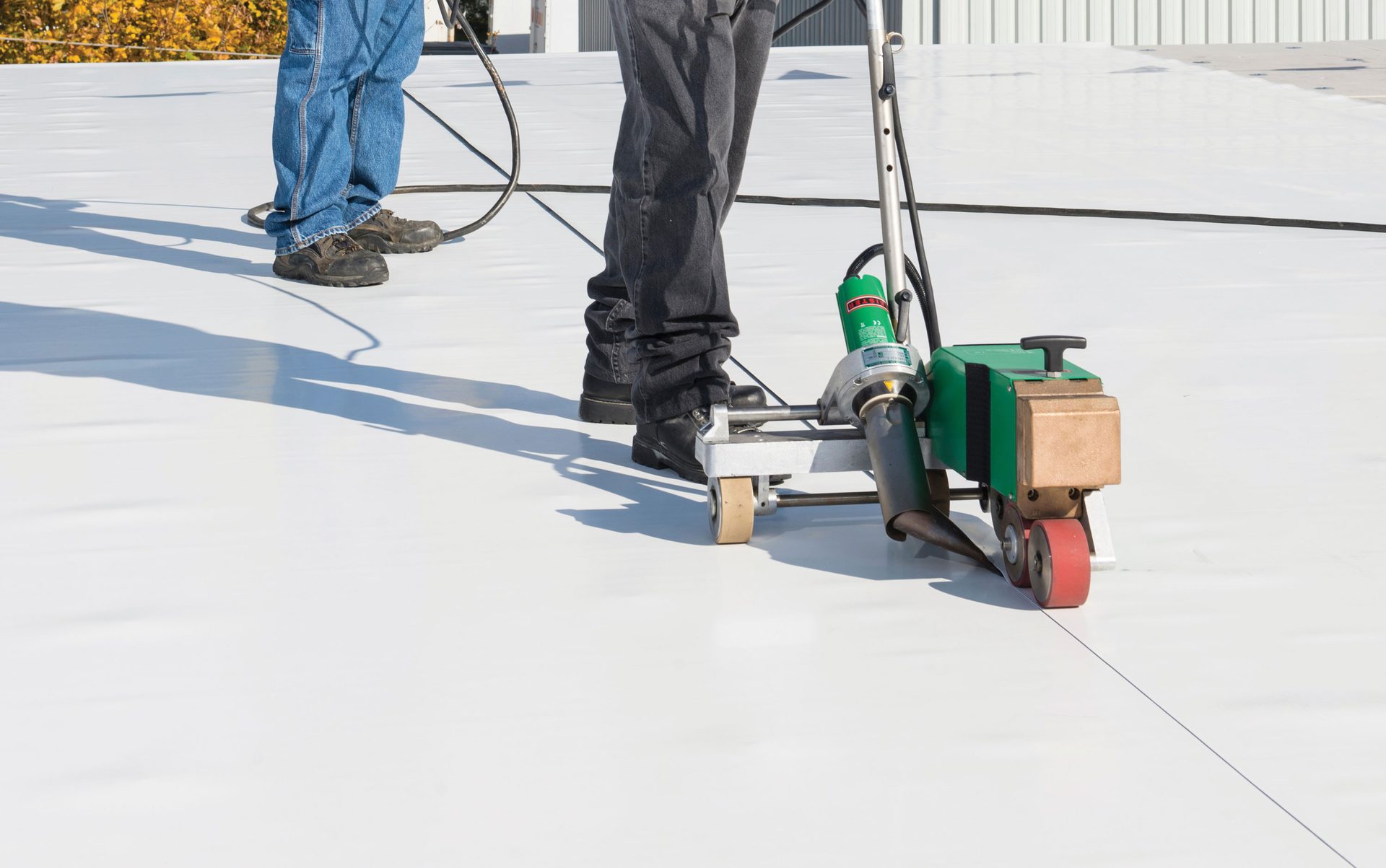
As with TPO roofing systems, PVC sheets are welded together to create exceptionally strong, waterproof seams. If done right, the seams will be stronger than the membranes themselves.
Polyester vs. Fiberglass Reinforcement
Under ASTM D4434 “Standard Specification for Poly (Vinyl Chloride) Sheet Roofing” – the ASTM International PVC roofing standard – PVC membranes must have a reinforced scrim. Reinforcement ensures the membrane has the weatherability needed to deliver long-term performance while still being flexible.
The reinforcement is either a polyester knit fabric or fiberglass. Polyester offers several big advantages.
- Puncture Resistance: Polyester-reinforced membranes are much more resistant to punctures than fiberglass-reinforced membranes, making them less likely to be damaged by debris, dropped tools, and foot traffic.
- Wind Uplift Performance: Polyester-reinforced membranes deliver significantly greater tearing strength and breaking strength than fiberglass-reinforced membranes. This means that more force would be needed to rip the membrane from an edge or make a small tear more significant, and more force would be required to break the membrane. These factors give them much better wind uplift performance in mechanically attached systems, where high winds and membrane flutter can create stress at the attachment points.
- Attachment Options: Polyester-reinforced membranes can be fully adhered or mechanically attached and be eligible for a no-dollar-limit (NDL) system warranty. Mechanical attachment of fiberglass-reinforced membranes is typically not allowed under manufacturers’ warranty requirements, mainly because of the wind uplift issues mentioned above.
Fiberglass-reinforced PVC membranes have better linear dimensional stability, meaning they contract and expand less over time. However, the advantage is only approximately one-third of 1%, providing no tangible benefit in fully adhered systems. When either type of membrane is subjected to dimensional change, the adhesive holds it securely in place. Years of use in the field demonstrate that fiberglass-reinforced PVC does not adhere better than polyester-reinforced PVC.
Type II vs. Type III vs. Type IV
ASTM D4434 creates three classifications for PVC roof membranes – Type II, Type III and Type IV. (When the standard was originally approved in 1985, Type I membranes also existed. However, they were typically not reinforced, often resulting in long-term performance issues. As a result, they were removed from the standard.)
Type II Membranes
The Type II membranes available today have fiberglass reinforcement. The testing required of Type II membranes demands a very marginal dimensional change in an aged membrane. The requirement is notably less demanding than other physical properties, such as puncture resistance, tearing strength, and breaking strength.
The minimum membrane thickness allowed is 45 mils.
Type III and Type IV Membranes
Today’s Type III and Type IV membranes are internally reinforced with polyester, increasing their tearing strength and breaking strength. As mentioned above, this is particularly important at the seam fastener and plate locations in mechanically attached systems, where high winds and membrane flutter may stress the membrane.
Type III and Type IV membranes also have significantly higher puncture resistance than Type II membranes.
The minimum allowable membrane thicknesses are 45 mils for Type III and 36 mils for Type IV. While ASTM D4434 allows Type IV membranes to be thinner than Type III membranes, most manufacturers’ products far exceed the 36-mil minimum requirement.
Type IV membranes must also meet more rigorous performance standards than Type III membranes. The minimum thresholds for Type IV membranes are 38% higher in breaking strength, 66% higher in elongation at break (how much the membrane can stretch before breaking) and 100% greater in tearing strength than for Type III membranes. Therefore, Type IV membranes are better equipped to withstand the tolls of real-world use and provide the strongest performance in mechanically attached systems.
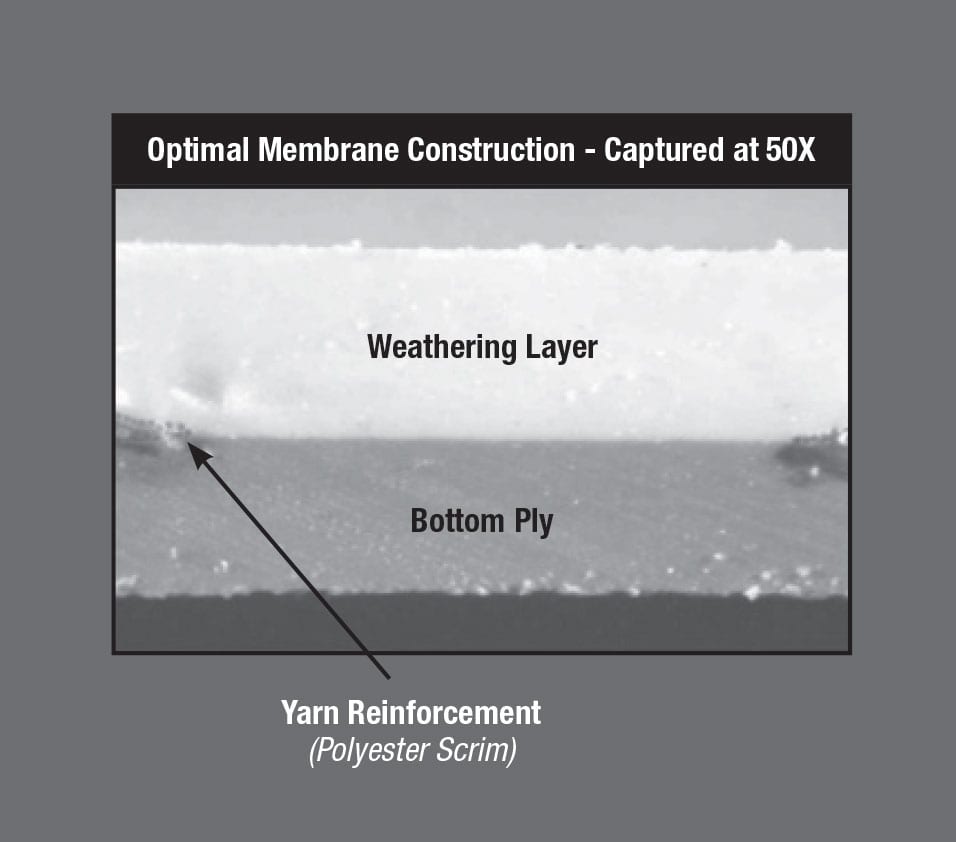
A sign of higher quality PVC is that the top and bottom plies are approximately the same thickness.
Optimal Membrane Construction
PVC roof membranes have two layers, with the scrim reinforcement placed between them. Fleece-backed and felt-backed membranes also have fleece or felt on the underside to allow other adhesive options, stronger adhesion, and improved performance in hail and puncture resistance areas.
The makeup of PVC membranes varies by manufacturer, but a sign of higher quality is that the top and bottom plies are approximately the same thickness. The top layer includes anti-weathering ingredients — such as antimicrobials, heat stabilizers and ultraviolet inhibitors — to ensure long-lasting performance. If it is significantly thinner than the bottom ply, the membrane will be far more prone to damage from abrasion scuffing. If the bottom layer is too thin, issues can result when welding the membrane, with the scrim being forced into the weld.
PVC KEE and PVC KEE HP Membranes
PVC KEE and PVC KEE HP membranes give contractors and designers additional options in tailoring solutions for jobs requiring a higher performance level.
PVC KEE
Plasticizers give PVC membranes the flexibility needed for use in roofing applications. In standard PVC membranes, all the plasticizer is liquid. Over the lifespan of the membrane, it migrates out, making the membrane more brittle.
In PVC KEE membranes, some of the liquid plasticizer is replaced with Dow ELAVOY Ketone Ethylene Ester (KEE), a solid, high-molecular-weight polymer. This gives PVC KEE membranes several performance advantages over standard PVC membranes:
- The KEE plasticizer does not migrate from the membrane, improving long-term flexibility.
- They are even more resistant to chemicals.
- They are more tolerant of extreme temperature swings.
- They better resist dirt pick-up, enhancing a roof’s aesthetics and, in the case of white membranes, helping them better retain their energy efficiency.
The PVC KEE membranes available today are classified as Type III and/or Type IV under ASTM D4434.
PVC KEE HP
PVC KEE HP (High-Performance) membranes use the KEE HP polymer, an upgrade to the KEE plasticizer used in PVC KEE membranes. KEE HP has an even higher molecular weight than standard KEE, so less plasticizer is needed to achieve the same performance characteristics.
KEE HP also increases seam weldability and keeps the membrane more flexible in cold temperatures.
The PVC KEE HP membranes available today are classified as Type III and/or Type IV under ASTM D4434.
KEE- and KEE HP-Modified PVC vs. KEE Sheets
PVC KEE and PVC KEE HP membranes are sometimes referred to as “KEE sheets.” They are, instead, KEE-modified PVC sheets.
True KEE sheets are not specified as PVC membranes under ASTM 4434 but under their own standard – ASTM D6754 “Standard Specification for Ketone Ethylene Ester Based Sheet Roofing.” Only a handful of manufacturers produce KEE sheets.
Under ASTM D6754, KEE must make up at least 50% of the membrane’s total polymer content by polymer weight. Adding this much KEE to the recipe has notable drawbacks.
Replacing so much liquid plasticizer with solid KEE significantly reduces the sheet’s weldability.
KEE costs more than liquid plasticizers. To bring the price of KEE membranes in line with that of KEE-modified PVC membranes, manufacturers often make the top layer thinner. As mentioned earlier, that can make the membrane more prone to abrasion damage.
Over five decades, PVC roofing systems have become a favorite choice of design professionals. Armed with a greater understanding of PVC roofing’s history, sustainability and performance characteristics, roofing contractors can be equally confident in recommending it to their customers.
Warranty Options
Contractors can offer customers various warranty options to meet their needs and budgets.
Material-only and NDL system warranties on commercial projects are available for various lengths of time. NDL warranties include labor and materials and are not limited to the original installed cost.
On residential jobs, material-only warranties covering various lengths of time are available.
Conclusion
Over five decades, PVC roofing systems have become a favorite choice of design professionals. Armed with a greater understanding of PVC roofing’s history, sustainability and performance characteristics, roofing contractors can be equally confident in recommending them to their customers. Membrane type, installation method, and warranty options abound, allowing contractors and their design partners to create roofing systems tailored to the specific requirements of each project.
Bryan Gottlieb is managing editor of Roofing Contractor. Reach him at 248-786-1591 or gottliebb@bnpmedia.com.
Art Aisner is editor-in-chief of Roofing Contractor. Reach him at aisnera@bnpmedia.com.
Tony Vieira is the product segment manager for low-slope roofing manufacturer Mule-Hide Products Co., where he oversees single-ply roofing, Poly ISO insulation, and cover boards product categories. Reach him at Tony.Vieira@mulehide.com.